Wheels in Motion: Winter Project Progress and A Look Forward
- gracemarietuttle
- Feb 3, 2024
- 3 min read
Team RLNT< here, back after the holidays! We are thrilled to update you on our progress as we embark on the next phase of our journey after successfully passing the design review in MECE 4340: Capstone 1. With the groundwork laid, we're now forging ahead with the production and validation of our Wheelchair Hill Assist Device.
During the winter break, our team made significant strides towards our project's progress. The team faced compatibility issues purchasing individual electrical components (motor hub, throttle, controller, cruise control). The team further researched and purchased a 36 [V] 350 [W] Electric Scooter Conversion DIY kit that contained all the required components. This kit allowed us to seamlessly connect the motor hub, controller, throttle, and cruise control to the battery. This kit saved the team substantial time and headaches, while not dramatically affecting the budget. The team wanted to ensure that the user interface would be able to be turned on and set to cruise control all by one hand's movement, allowing the user to be still able to steer the wheelchair, which is possible through the purchased kit. The connected electronics assembly with the motor hub test stand can seen below in Figure 1.

Figure 1: Electronics assembly of the device with labeled critical components.
To facilitate basic functionality testing of the kit, Team RLNT< crafted a basic 3D-printed test stand as shown in Figure 2. The team then wired the electronics and witnessed the motor hub spinning. The team also tested the basic functionality of the cruise control buttons.
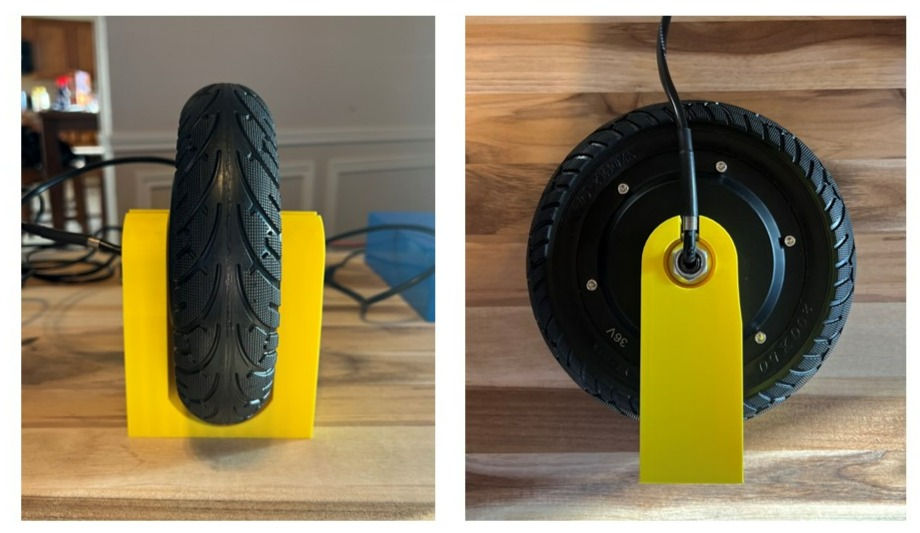
Figure 2: Front and side views of the 3D printed motor hub test stand.
The team refined the CAD model of the device's shell, reinforcing identified weak points by increasing thickness and inlay percentage. The overall device will be printed at 25% inlay. The team made modifications to all bolt holes to be printed at 100% inlay, including the bolt hole and surrounding areas for the hub motor. Team RLNT< also increased the inlay of the device's shell legs to 50% to account for the weight of the battery. The team also increased the width of the wheelie bar attachment arm extrusion, as shown in Figure 3 (width indicated by the red arrow). Team RLNT< 3D printed small sections of the device's shell to ensure proper dimensioning was used in critical sections. The device's shell and arms will take over 35 hours to print and cost over $45 for one iteration, so the team is doing as much analysis as possible to ensure the device will not have to be printed multiple times. The team is currently in the process of final print specification setting changes before 3D printing the shell and arms.

Figure 3: Location of the increased wheelie bar attachment arm extrusion width.
Looking ahead to the next work period, our major milestone is the 3D printing of the device's shell and arms, and purchasing the remainder of our required items for validation. 3D printing the device's shell and arms is critical as then we will be ready to assemble the entire device. The team has selected all of the materials needed, and just needs to place the order for the validation equipment as well as some fasteners. Due to increasing the width of the wheelie bar attachment arm extrusion, the team will need to make adjustments and purchase new fasteners.
Over the next two weeks, Team RLNT<'s focus is on orchestrating the 3D printing of the device and arms. Team member Jakob Lee, purchased a 3D printer at the beginning of last semester for the team to be able to print their device with. The device's shell and arms will be printed in ASA filament which poses an issue since it releases toxic fumes when printed. Additionally, the total print time exceeds 35 hours. The 3D printer is located inside Jakob's home office where he completes his school work. Due to the toxicity, Jakob will have to close off the room for almost two days, which is inconvenient for his studies. The team is considering moving the 3D printer to another location but is having difficulties determining a private climate-controlled location where the printer can be left undisturbed during the total print time.
Team RLNT< remains committed to overcoming these obstacles and ensuring their project's success. The team is currently roughly two weeks ahead of schedule and will use this extra time to determine how to navigate these problems. Stay tuned for more updates as the team works towards a functioning prototype!
Comments